Felisha Vestal: “Transplant” to Ag Formulates Success in the Field
Chemical engineer learns to “speak ag,” embraces the mission.
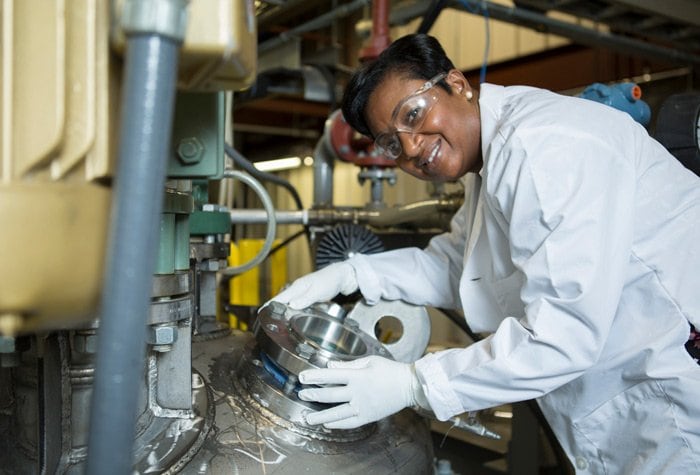
Unlike many Syngenta employees, Felisha Vestal didn’t grow up on a farm. Trained as a chemical engineer, she’s more of a “transplant” to agriculture, with roots that nonetheless have grown deep.
Vestal moved from AstraZeneca pharmaceuticals to Syngenta in 2001, shortly after the new company was created. She was quick to notice that working in agriculture felt different, though. The mission of helping to feed the world had an urgency that was more personal to her.
“It’s not that pharmaceuticals aren’t important—they certainly are,” says Vestal. “But agriculture is a different challenge in that there has to be enough. How do we produce enough to feed the world’s growing population?”
Formulation Engineering
Vestal grew up in a military family, which meant frequent moves around the U.S. and to such far-flung places as Panama and South Korea. When she was in the eighth grade, the family settled for good in Goldsboro, North Carolina. When it was time to go to college, she chose North Carolina Agriculture & Technical State University because of its chemical engineering program. After graduating in 1991, she quickly found employment in the industry.
At the time, she’d had no exposure to agriculture. “Chemical engineering doesn’t speak ag,” she says. “It’s all about manufacturing—how do you build a manufacturing plant to make products to exact specifications, safely and as efficiently as possible?”
The formulation engineers on Vestal’s team then take the chemists’ formulation and figure out how to replicate it in commercial quantities. The ideal formulation must maximize the a.i.’s performance and be stable, safe and convenient to store, mix and apply.
Scaling Up
“Our challenge is to take something the chemists mix by hand in a beaker and scale it up to manufacturing hundreds of thousands of gallons in a commercial plant,” Vestal explains. (That’s more than a millionfold increase.) “And the commercial product must be exactly the same as the formulation in the beaker with zero deviation.”
In case that doesn’t sound difficult enough, consider that crop protection products often mix solid and liquid a.i.s, or a.i.s that are otherwise incompatible. In addition to pure volume, variables—such as temperature, speed of mixing, order of mixing, and materials used in tanks and pipes—can all affect the formulation process.
Then, the products are shipped long distances, exposed to extreme temperatures, and stored for months or even years. When it comes time to use them on farms, they’re mixed with a variety of ingredients, including water, fertilizers and other formulated pesticides. And they must come out of the spray nozzles cleanly and uniformly.
“There’ll always be many issues in the scale-up,” Vestal says. “We have to look at all possibilities, generate lots of data and really get down into the details.”
“That Was Exciting!”
Vestal lights up as she talks about taking on complex challenges, though. Her team recently worked on a seed treatment product with seven a.i.s, which must be applied in tiny, precise quantities to the seeds. “It’s the joy of solving problems,” she says. “That was excellent! That was exciting!”
Vestal’s team uses a pilot plant at its Greensboro, North Carolina, location as an intermediate proving ground between the beaker and the commercial plant. It can run batches or continuous formulation processes at roughly one-tenth the scale of manufacturing. There are vessels of up to 250 gallons and pipes running around the room.
Eventually, the engineer will travel to the commercial plant to work with the staff there on the ultimate scale-up. “You stay there until you get it right,” she says. They also travel to distributor and retailer sites to get input from customers and to consult on storage and handling facilities.
Outperforming the Competition
Vestal describes her job in a nutshell as making sure her team has the right tools and resources to help ensure the best possible formulations reach customers and deliver results in the field.
She takes pride in the 16 products Syngenta launched in 2016—with no significant formulation issues when the products hit the field.
“That was gratifying,” she says. “We want to ensure that Syngenta products solve problems for our customers and outperform the competition. Syngenta has committed to providing sustainable solutions and to equipping farmers to provide food and fuel for many generations to come. It’s our goal and our mission.”
Vestal moved from AstraZeneca pharmaceuticals to Syngenta in 2001, shortly after the new company was created. She was quick to notice that working in agriculture felt different, though. The mission of helping to feed the world had an urgency that was more personal to her.
“It’s not that pharmaceuticals aren’t important—they certainly are,” says Vestal. “But agriculture is a different challenge in that there has to be enough. How do we produce enough to feed the world’s growing population?”
Formulation Engineering
Vestal grew up in a military family, which meant frequent moves around the U.S. and to such far-flung places as Panama and South Korea. When she was in the eighth grade, the family settled for good in Goldsboro, North Carolina. When it was time to go to college, she chose North Carolina Agriculture & Technical State University because of its chemical engineering program. After graduating in 1991, she quickly found employment in the industry.
At the time, she’d had no exposure to agriculture. “Chemical engineering doesn’t speak ag,” she says. “It’s all about manufacturing—how do you build a manufacturing plant to make products to exact specifications, safely and as efficiently as possible?”
At Syngenta, Vestal immersed herself in ag, working as a hands-on formulation engineer for 10 years. Because of her leadership in this field, she is now manager of the Technology Finished Product Process group, a team of engineers and technicians who work closely with formulation chemists. As a single or combination of active ingredients (a.i.s) is finalized for a new product, formulation chemists work on combining these ingredients with inert ingredients. The chemists create the formulation that retailers, applicators and farmers will use to deliver the a.i.s to pest targets in the field.“Our challenge is to take something the chemists mix by hand in a beaker and scale it up to manufacturing hundreds of thousands of gallons in a commercial plant. And the commercial product must be exactly the same as the formulation in the beaker with zero deviation.”
The formulation engineers on Vestal’s team then take the chemists’ formulation and figure out how to replicate it in commercial quantities. The ideal formulation must maximize the a.i.’s performance and be stable, safe and convenient to store, mix and apply.
Scaling Up
“Our challenge is to take something the chemists mix by hand in a beaker and scale it up to manufacturing hundreds of thousands of gallons in a commercial plant,” Vestal explains. (That’s more than a millionfold increase.) “And the commercial product must be exactly the same as the formulation in the beaker with zero deviation.”
In case that doesn’t sound difficult enough, consider that crop protection products often mix solid and liquid a.i.s, or a.i.s that are otherwise incompatible. In addition to pure volume, variables—such as temperature, speed of mixing, order of mixing, and materials used in tanks and pipes—can all affect the formulation process.
Then, the products are shipped long distances, exposed to extreme temperatures, and stored for months or even years. When it comes time to use them on farms, they’re mixed with a variety of ingredients, including water, fertilizers and other formulated pesticides. And they must come out of the spray nozzles cleanly and uniformly.
“There’ll always be many issues in the scale-up,” Vestal says. “We have to look at all possibilities, generate lots of data and really get down into the details.”
“That Was Exciting!”
Vestal lights up as she talks about taking on complex challenges, though. Her team recently worked on a seed treatment product with seven a.i.s, which must be applied in tiny, precise quantities to the seeds. “It’s the joy of solving problems,” she says. “That was excellent! That was exciting!”
Vestal’s team uses a pilot plant at its Greensboro, North Carolina, location as an intermediate proving ground between the beaker and the commercial plant. It can run batches or continuous formulation processes at roughly one-tenth the scale of manufacturing. There are vessels of up to 250 gallons and pipes running around the room.
Eventually, the engineer will travel to the commercial plant to work with the staff there on the ultimate scale-up. “You stay there until you get it right,” she says. They also travel to distributor and retailer sites to get input from customers and to consult on storage and handling facilities.
Outperforming the Competition
Vestal describes her job in a nutshell as making sure her team has the right tools and resources to help ensure the best possible formulations reach customers and deliver results in the field.
She takes pride in the 16 products Syngenta launched in 2016—with no significant formulation issues when the products hit the field.
“That was gratifying,” she says. “We want to ensure that Syngenta products solve problems for our customers and outperform the competition. Syngenta has committed to providing sustainable solutions and to equipping farmers to provide food and fuel for many generations to come. It’s our goal and our mission.”