Superior Packaging Enhances Safety and Sustainability
Cutting-edge technology and standard-setting tests make Syngenta packaging uniquely superior.
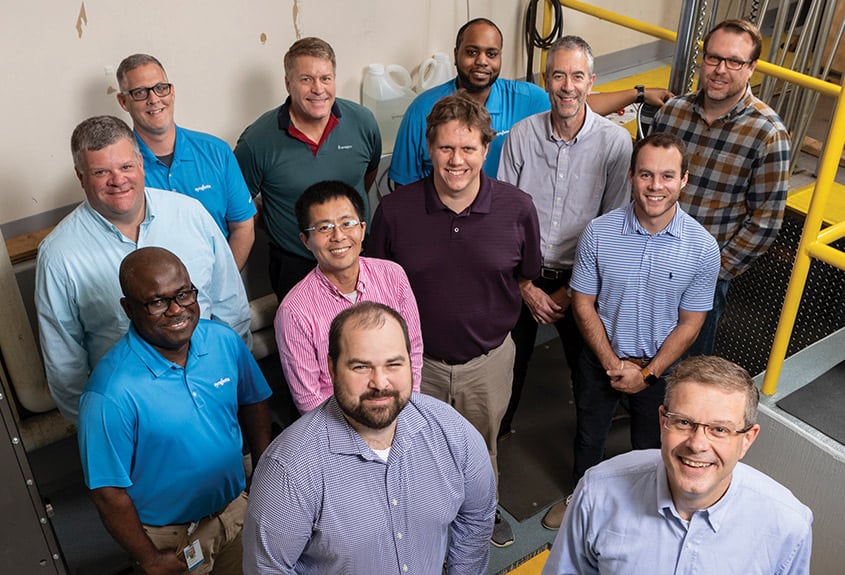
The first indication of product quality any customer sees is packaging. It shows how a product has handled the rigors of shipping and how much the manufacturer cares about providing quality from conceptualization to end use.
“When you receive a product in a quality package, it makes you feel that what’s inside is going to perform well,” says Eric Hoene, a branch manager for Premier Ag in Seymour, Indiana. “I believe Syngenta takes pride not only in the products it sells, but also in the appearance and durability of the packages that contain those products.”
Syngenta follows a customer-first approach when it comes to developing its packaging, always keeping growers’ and resellers’ safety and convenience top of mind. Its investment in this area is a testament to that commitment. “Syngenta remains among the only ag chemical companies in the U.S. with an in-house packaging test lab, and we believe ours is by far the most advanced,” says Fábio Gimenes, the formulation and packaging engineering head of Syngenta in North America. “Our full-service process sets the industry standard and ensures customers get the best packaging available in the industry.”
Certified and Ready
The Syngenta lab isn’t only one of a few in the industry. It also has full approval from the U.S. Department of Transportation (USDOT) and the International Safe Transit Association (ISTA) to self-UN (United Nations) certify packaging. These endorsements mean Syngenta engineers are licensed to approve packaging for products themselves. As a result, the company can produce higher quality products for its customers, Gimenes says, since engineers can continuously work on refinements and improvements, instead of waiting for an outside firm to complete a separate certification process.
With the USDOT and ISTA certifications in hand, Syngenta runs a full spectrum of individual assessments. These include tests for enduring the traumas that are part of the real-life shipping process, such as:
The lab also has equipment for advanced vibration tests beyond what most test labs can do, according to Josh House, packaging test specialist at Syngenta. “There are specific tests we run for transport by truck, rail, air and ocean,” he says. “With random vibration profiles, we simulate a package’s experience on a plane or inside an ocean shipping container. This allows us to go deeper than results we would get from a standard shaker-table.”
The technology in the testing lab can actually speed up the manufacturing process, since high-quality packaging that the manufacturing plants need to contain products is more readily available. Among the most important pieces of equipment that increase speed and efficiency are the lab’s 3D printers. These printers allow Syngenta to reduce the need for third-party designers and fabricators. By keeping even more of the process in-house, engineers can design and produce physical testing models within days instead of weeks or months.
This technology has substantial benefits for growers who use Syngenta products, according to Kal Edly, Syngenta 3D printing specialist. “We’re able to give end users tailored features, based on their feedback, that may have previously been cost prohibitive,” he says. “Since we’re able to produce prototypes more cost efficiently, we can quickly make changes and hone in on the exact features that customers want.”
Other technologies also play important roles in the testing process. Slow-motion cameras, for example, allow enhanced analysis of test results. The lab’s cameras also use a machine learning program, which improves their accuracy when checking package labels for errors mechanically. In the 25 years since the lab opened, new equipment has also expanded the lab’s capability to test seed bags and drums.
The battery of tests and innovations that go into the Syngenta packaging process means better end products and happier customers. “When I receive a shipment from Syngenta, I know that I’m getting a quality product in a package that will meet my needs and the needs of growers in my area,” Hoene says.
Sustainable and Strong
Superior packaging uses plastics and other materials sustainably. For instance, Syngenta packaging incorporates protection against ultraviolet radiation, which can degrade product quality.
To improve sustainability across its supply chain, Syngenta recently announced a $2 billion investment in sustainable agriculture. Part of this investment will go toward packaging innovations.
“Things like reducing the weight of plastic in containers, moving plastics and products in bulk, and cutting the thickness of our label paper all contribute to making our operations more sustainable,” says Gabriel Oxby, Syngenta formulation and packaging group leader.
Syngenta hopes that these and other sustainability efforts will help the company meet its target to reduce the carbon intensity of its operations by 50% by 2030.
“From lab to field, we help make sure our products arrive to our customers intact and on time, ready to go to work,” Oxby says.
The first indication of product quality any customer sees is packaging, according to @SyngentaUS.
click to tweet
“When you receive a product in a quality package, it makes you feel that what’s inside is going to perform well,” says Eric Hoene, a branch manager for Premier Ag in Seymour, Indiana. “I believe Syngenta takes pride not only in the products it sells, but also in the appearance and durability of the packages that contain those products.”
Syngenta follows a customer-first approach when it comes to developing its packaging, always keeping growers’ and resellers’ safety and convenience top of mind. Its investment in this area is a testament to that commitment. “Syngenta remains among the only ag chemical companies in the U.S. with an in-house packaging test lab, and we believe ours is by far the most advanced,” says Fábio Gimenes, the formulation and packaging engineering head of Syngenta in North America. “Our full-service process sets the industry standard and ensures customers get the best packaging available in the industry.”
Certified and Ready
The Syngenta lab isn’t only one of a few in the industry. It also has full approval from the U.S. Department of Transportation (USDOT) and the International Safe Transit Association (ISTA) to self-UN (United Nations) certify packaging. These endorsements mean Syngenta engineers are licensed to approve packaging for products themselves. As a result, the company can produce higher quality products for its customers, Gimenes says, since engineers can continuously work on refinements and improvements, instead of waiting for an outside firm to complete a separate certification process.
With the USDOT and ISTA certifications in hand, Syngenta runs a full spectrum of individual assessments. These include tests for enduring the traumas that are part of the real-life shipping process, such as:
- Drop tests to establish the height from which a package can fall without breaking, by using platforms that are quickly pulled away to replicate sudden drops;
- Compression tests, which simulate stacking packages on top of each other, as in a warehouse, by measuring a package’s response to constant pressure from a machine in the lab; and
- Horizontal impact tests, which use lab devices to gauge how well packages can withstand such horizontal impacts as rail car coupling, rough forklift handling and truck docking.
The lab also has equipment for advanced vibration tests beyond what most test labs can do, according to Josh House, packaging test specialist at Syngenta. “There are specific tests we run for transport by truck, rail, air and ocean,” he says. “With random vibration profiles, we simulate a package’s experience on a plane or inside an ocean shipping container. This allows us to go deeper than results we would get from a standard shaker-table.”
On the Cutting Edge“Syngenta remains among the only ag chemical companies in the U.S. with an in-house packaging test lab, and we believe ours is by far the most advanced.”
The technology in the testing lab can actually speed up the manufacturing process, since high-quality packaging that the manufacturing plants need to contain products is more readily available. Among the most important pieces of equipment that increase speed and efficiency are the lab’s 3D printers. These printers allow Syngenta to reduce the need for third-party designers and fabricators. By keeping even more of the process in-house, engineers can design and produce physical testing models within days instead of weeks or months.
This technology has substantial benefits for growers who use Syngenta products, according to Kal Edly, Syngenta 3D printing specialist. “We’re able to give end users tailored features, based on their feedback, that may have previously been cost prohibitive,” he says. “Since we’re able to produce prototypes more cost efficiently, we can quickly make changes and hone in on the exact features that customers want.”
Other technologies also play important roles in the testing process. Slow-motion cameras, for example, allow enhanced analysis of test results. The lab’s cameras also use a machine learning program, which improves their accuracy when checking package labels for errors mechanically. In the 25 years since the lab opened, new equipment has also expanded the lab’s capability to test seed bags and drums.
The battery of tests and innovations that go into the Syngenta packaging process means better end products and happier customers. “When I receive a shipment from Syngenta, I know that I’m getting a quality product in a package that will meet my needs and the needs of growers in my area,” Hoene says.
Sustainable and Strong
Superior packaging uses plastics and other materials sustainably. For instance, Syngenta packaging incorporates protection against ultraviolet radiation, which can degrade product quality.
To improve sustainability across its supply chain, Syngenta recently announced a $2 billion investment in sustainable agriculture. Part of this investment will go toward packaging innovations.
“Things like reducing the weight of plastic in containers, moving plastics and products in bulk, and cutting the thickness of our label paper all contribute to making our operations more sustainable,” says Gabriel Oxby, Syngenta formulation and packaging group leader.
Syngenta hopes that these and other sustainability efforts will help the company meet its target to reduce the carbon intensity of its operations by 50% by 2030.
“From lab to field, we help make sure our products arrive to our customers intact and on time, ready to go to work,” Oxby says.